Future-proof plant operation with Monitoring-as-a-Service
“INNIO Group’s Jenbacher myPlant Performance platform and myPlant Customer Connect App have been crucial to the economic operation of our plant, and also a flagship project for intelligent plant management."
Frank Rümper, Asset manager at Avacon Natur, Germany
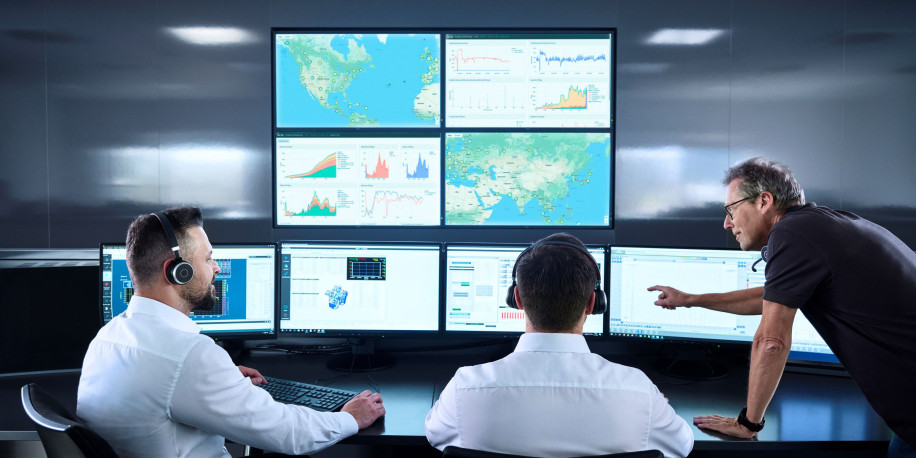
Background
Modern plant control systems capture, process, and generate a seemingly overwhelming volume of data, which, at first glace, demands considerable expertise and time for analysis. For the operating personnel on site, this brings correspondingly great challenges. For this reason, automated analyses of the operating status and easy access to expert knowledge are increasingly becoming the focus of economically successful plant management, particularly in light of the growing scarcity of skilled workers.
Avacon Natur operates more than 300 energy plants with an electrical output of more than 44 megawatts, generating more than 330 gigawatt hours of heat and 190 gigawatt hours of electricity annually. The plants are using INNIO's Jenbacher myPlant Performance remote plant monitoring platform to provide real-time data for their operations. The high availability of Avacon's plants is further enhanced by an in-house team responsible for plant maintenance and repairs, ensuring exceptional service quality.
Solution
Working with Avacon Natur at its Salzwedel combined heat and power (CHP) plant, INNIO successfully completed a project for the automated, proactive use of plant data based on INNIO's digital myPlant Performance platform. The project resulted in the Monitoring-as-a-Service (MaaS) concept.
New algorithms are analyzing data to enable the company to react quickly to changing trends or anomalies. INNIO's Jenbacher customer service representatives generate and proactively forward individual suggestions for solutions or improvements to Avacon. Jenbacher experts also are available for a comprehensive plant analysis, taking into account the complete engine history. Operating personnel also benefit from the myPlant Customer Connect App by receiving push notifications with suggestions for improvement, such as optimizing plant performance or increasing efficiency. In addition, the app facilitates direct contact with the Jenbacher Service team, allowing the company to swiftly make decision that positively impact operating results in an even shorter timeframe.
By simplifying communication with INNIO, the MaaS concept helps operators quickly identify optimization potential for their energy solutions and effectively capitalize on them in a resource-efficient manner.
Result
Reliable operating data are needed to increase the economic efficiency of CHP plants, and to expand the role of such plant in the power and heat sector. By linking historical data with forecasts of future behavior, deviations can be detected in advance and measures can be taken at an early stage to avoid shutdowns. Modern automated methods and proactive analysis by engine experts actively support plant operator in improving efficiency, thereby contributing to a positive operating result.
With the innovative Jenbacher myPlant Performance technology, INNIO and Avacon Natur have shown that algorithm-assisted plant management on an industrial scale can be implemented today, setting the course for a greener, safer, more economical, and future-oriented energy supply.
At the Salzwedel plant's CHP module, data points from the Jenbacher DIA.NE XT engine control system helped the operators recognize that an increase in efficiency would be possible through modifications in mixture formation. Corresponding adjustments were successfully carried out during the following maintenance event.
Customer benefits
- Support for operational management by means of intelligent algorithms .
- Plant analysis by means of modern diagnostic technology.
- Cost reduction through proactive 24/7 online monitoring by a dedicated team of experts from the original manufacturer.
- Tailored upgrade recommendations based on analyzer-specific engine data.
- Direct access to the Jenbacher Technical Support team via INNIO's myPlant Customer Service App.
- Reduction of unplanned downtime and early detection of deviations even before they become noticeable.
Media